What works in Industrial IoT: lessons from real-world smart factories
by Manuel Gawert on Jun 30, 2025
Walk into any modern factory, and you’ll likely witness a jarring paradox: gleaming digital dashboards displaying real-time metrics — while operators a few steps away make critical decisions using printed spreadsheets. This isn't just a technology disconnect — it’s the visible symptom of the chasm between digital transformation theory and manufacturing reality.
With deep experience in the manufacturing trenches, we've collected battle-tested insights about what actually moves the needle in smart factory initiatives. Not just what should work according to PowerPoint presentations, but what truly transforms operations when rubber meets road.
The digital manufacturing disconnect
Despite the promise of digital transformation, factory floors often resemble a technological patchwork quilt rather than a unified system. Several recurring barriers continue to stall progress:
The language barrier of machines
Today’s factories run a hodgepodge of machines — some new, some pushing retirement age. That’s not surprising. But what’s more problematic is this: even machines from the same vendor, doing the same job, can speak different languages depending on the year they were purchased. One CNC machine might output structured OPC-UA messages, while another from five years earlier spits out raw serial data. This protocol fragmentation creates tangled data silos that make integration feel less like engineering and more like archaeology.
When IT and OT speak different languages
Information Technology (IT) focuses on secure architectures and system governance. Operations Technology (OT) obsesses over uptime, cycle times, and on-the-floor continuity. When these two groups are forced together without a common framework, friction follows. Too often, their digital initiatives ignite debates — instead of innovation.
Trapped in pilot purgatory
The manufacturing landscape is full of dazzling demos and promising pilots that never make it past PowerPoint. These "successful" proofs of concept look great in isolated environments but collapse under the weight of real-world variability when asked to scale. When everything works perfectly in a lab but fails in production, trust erodes — and transformation stalls.
Drowning in data, starving for action
Factories have grown adept at collecting oceans of data, but turning that data into action remains elusive. Without actionable insights, dashboards become expensive wall decorations — and digitization becomes a cosmetic upgrade rather than an operational shift.
Patterns from the front lines
In this challenging landscape, we've observed clear patterns among manufacturers who transcend the obstacles:
Hybrid teams with hybrid DNA
When manufacturing veterans and technology specialists work under shared objectives, magic happens. These cross-functional teams bridge the knowledge gap between what’s technically possible and what’s operationally valuable.
One precision components manufacturer we work with created what they call their “digital bridge team” — a unit combining production engineers who understand the rhythms of the shop floor with IT specialists who know how to harness data. Their predictive maintenance system succeeded where previous attempts failed because it respected both technical requirements and operational realities.
The problem-obsessed approach
The most transformative digital initiatives begin with operational challenges — not technology catalogues. This relentless focus on real problems creates solutions people actually use rather than systems they're forced to adopt.
One team started with a deceptively simple question: “Why does Line 2 consistently outperform Line 1 despite identical equipment?” Their data analytics revealed previously invisible micro-stoppages plaguing Line 1. Fixing these hidden issues boosted performance dramatically — and turned skeptical operators into digital champions.
The Goldilocks zone of standardization
Smart factory leaders have discovered that neither rigid standardization nor unconstrained flexibility works. Instead, they create what one manufacturer calls their “Goldilocks architecture” — standardized where it matters, flexible where it counts:
-
Infrastructure: Highly standardized and centrally managed
-
Data models: Consistent frameworks with adaptable elements
-
Applications: Flexible implementation within clear guardrails
This balanced approach creates a foundation solid enough to scale — but adaptable enough to address unique operational needs.
Integration layers that unlock hidden value
Forward-thinking manufacturers are creating abstraction layers that transform the babble of machine languages into standardized data streams. These integration platforms decouple physical equipment from business applications — dramatically simplifying future connections.
Rather than building custom integrations for each new use case, these manufacturers invest once in a platform that handles the complexity of machine communication — allowing them to rapidly develop new applications without rebuilding connectivity each time.
Value that speaks to every stakeholder
The most successful digital initiatives directly address the daily pain points of each user group. For maintenance teams, it might be predicting failures before they happen. For operators, it could be eliminating tedious manual data entry. For managers, perhaps it’s real-time visibility into production bottlenecks.
When digital solutions solve actual problems for real people, adoption becomes a natural response — rather than a change management challenge.
The Giant Swarm difference: unifying the factory floor
Already proven in the field, our Giant Swarm Industrial Internet of Things (IIoT) Platform was built from the ground up based on hard-won lessons from real manufacturers. It’s not a prototype — it’s powering digital transformation today by bridging the persistent gaps that stall most smart factory efforts.
Unified without uniformity
Our platform integrates diverse factory environments into a cohesive ecosystem — without forcing a one-size-fits-all approach. This means you can connect everything from legacy equipment to cutting-edge robotics — without ripping and replacing functional systems.
Edge intelligence, cloud power
Manufacturing data needs both local responsiveness and global analytics. Our platform processes information where it makes the most sense — time-sensitive operations at the edge, complex analytics in the cloud — creating a seamless continuum that optimizes both performance and insight.
Focus on innovation, not infrastructure
Your engineers should be solving manufacturing challenges — not wrestling with infrastructure. We handle the technical complexity of platform operations, security, and scaling — freeing your team to focus on what actually drives competitive advantage.
Open source, closed loop
Built on Kubernetes and cloud native technologies, our platform gives you the freedom of open source — without the integration headaches. You avoid vendor lock-in while gaining a consistent, reliable operational experience across all manufacturing environments.
Weeks, not years
Most importantly, our approach delivers tangible results in weeks — rather than years. No more extended implementation timelines with value perpetually over the horizon — our platform comes pre-configured to enable rapid adoption with immediate operational impact.
Evolving the Industrial IoT playbook
As manufacturing technology continues advancing, we’re developing new perspectives on what drives successful digital transformation:
-
Standardize the foundation, not the ceiling — The most innovative manufacturers create consistent technological foundations while encouraging creative applications that address unique operational needs.
-
End-to-end visibility transforms decision-making — When data flows seamlessly from production through supply chain, quality, and customer feedback, manufacturers gain unprecedented ability to optimize across traditional boundaries.
-
The compound interest of digital transformation — While direct efficiency gains matter, the compounding effects of better decision-making, faster problem-solving, and increased organizational agility deliver the most significant long-term returns.
A truly smart factory isn't just a collection of connected machines — it’s an environment where data flows effortlessly across traditional boundaries to drive better decisions at every level. By focusing on both technological architecture and human factors, manufacturers can transform not just their operations — but their competitive position.
Curious how leading manufacturers are turning vision into value? Let’s talk.
You May Also Like
These Related Stories
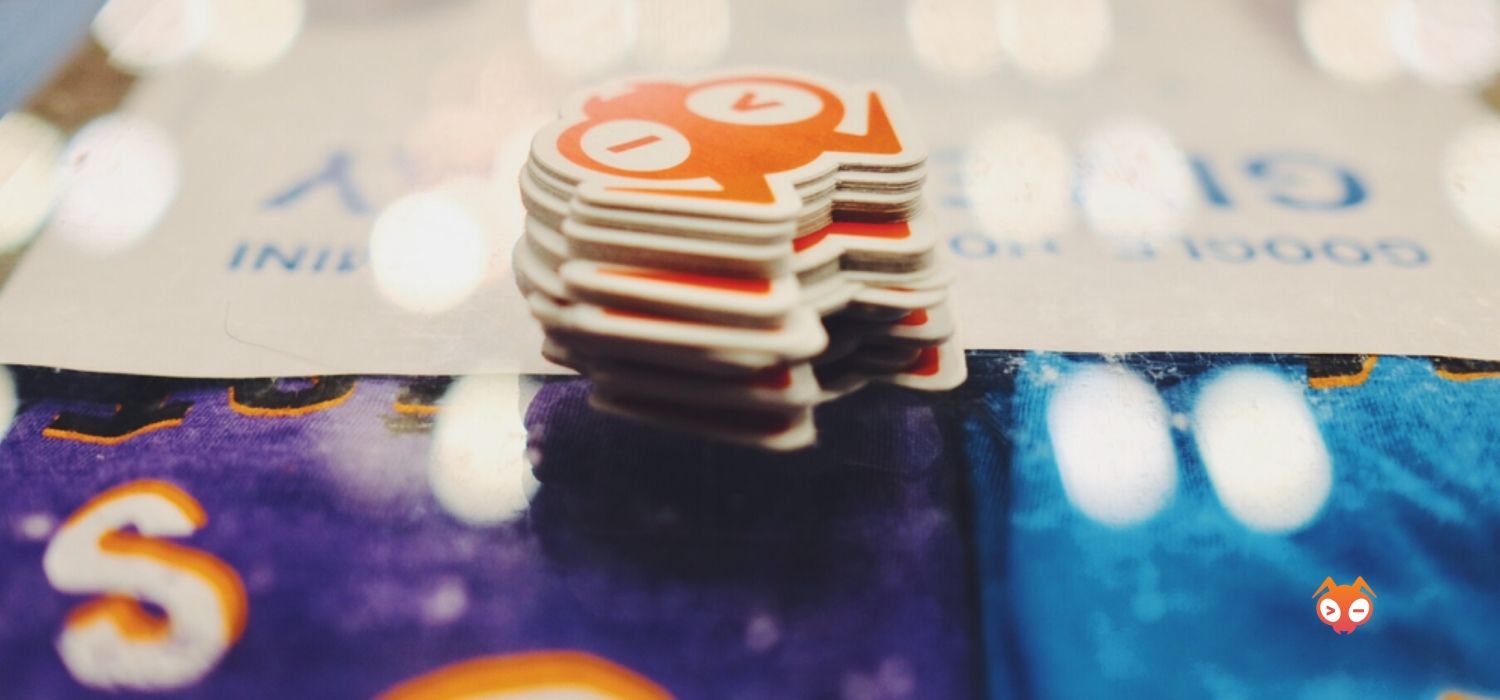
My first year @ Giant Swarm
Expectations vs. Reality Having been part of the swarm for a year now, I would like to share some insights regarding my expectations before starting a …
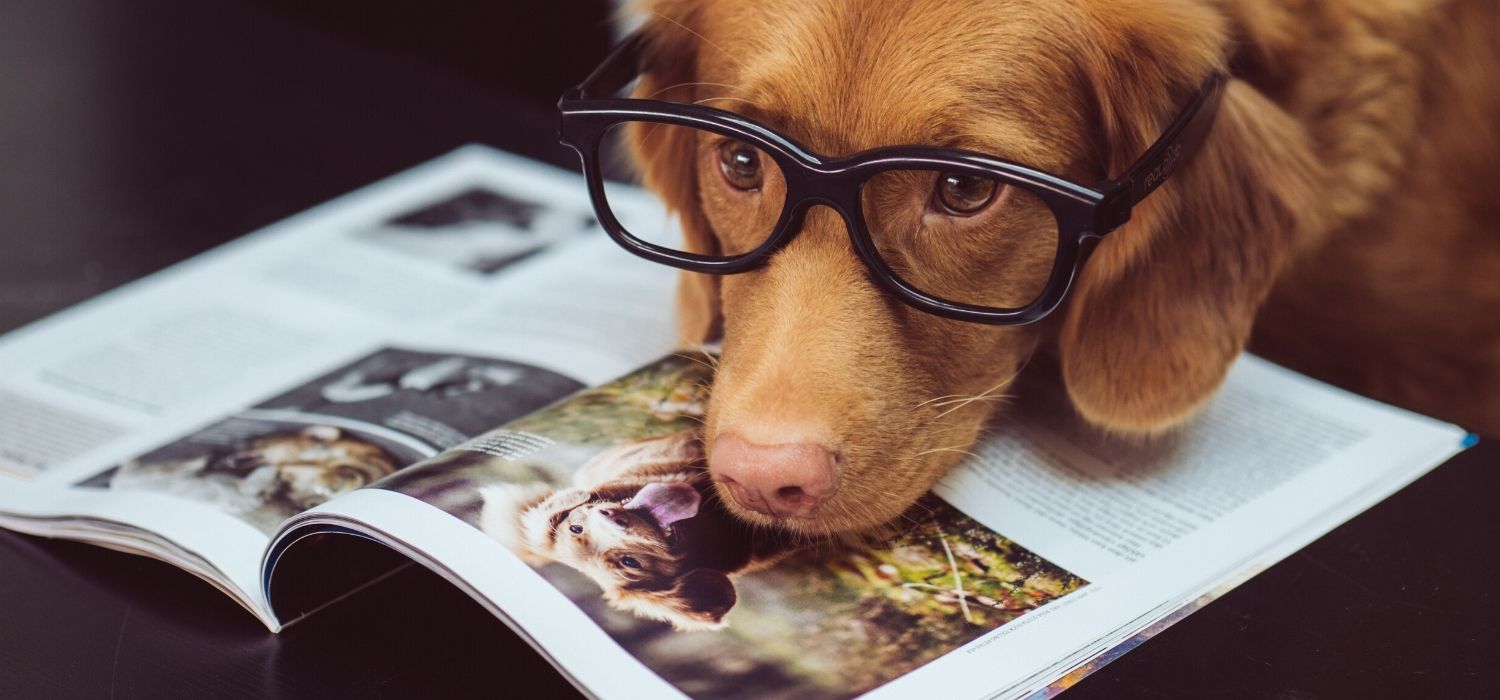
Remote Work Is Not the Same As Working from Home
This year's COVID-19-induced lockdown has meant that many of my friends have started adjusting to a way of working that we consider to be the standard …
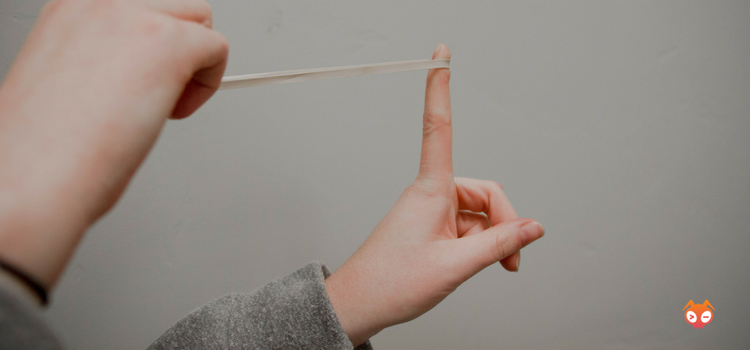
Reliability Is Not Enough - Building Resilient Applications With Containerized Microservices
When we talk about applications and their deployment in production, we often talk about reliability as a non-functional requirement. What is it that w …